Plastic extrusion for tubing, profiles, and custom shapes
Plastic extrusion for tubing, profiles, and custom shapes
Blog Article
Understanding the Basics and Applications of Plastic Extrusion in Modern Manufacturing
In the realm of modern production, the method of plastic extrusion plays an important duty - plastic extrusion. This intricate procedure, entailing the melting and shaping of plastic through specialized dies, is leveraged throughout numerous sectors for the production of varied items. From vehicle parts to customer items packaging, the applications are vast, and the possibility for sustainability is similarly outstanding. Unraveling the basics of this process exposes the true versatility and capacity of plastic extrusion.
The Fundamentals of Plastic Extrusion Refine
While it may show up complicated, the principles of the plastic extrusion process are based on reasonably simple principles. It is a manufacturing process where plastic is thawed and then shaped into a continual account through a die. The plastic extrusion procedure is extensively used in various markets due to its adaptability, cost-effectiveness, and efficiency.
Various Kinds Of Plastic Extrusion Techniques
Structure upon the basic understanding of the plastic extrusion process, it is required to check out the numerous strategies included in this manufacturing method. In contrast, sheet extrusion develops huge, level sheets of plastic, which are typically further processed into items such as food product packaging, shower drapes, and auto parts. Understanding these strategies is vital to using plastic extrusion effectively in modern production.
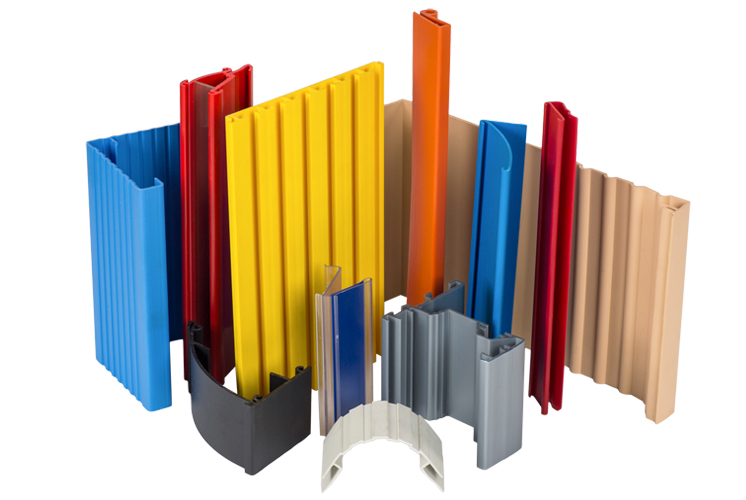
The Duty of Plastic Extrusion in the Automotive Industry
An overwhelming bulk of components in modern-day cars are items of the plastic extrusion procedure. This procedure has revolutionized the automotive sector, changing it into an extra effective, affordable, and adaptable manufacturing market. Plastic extrusion is largely used in the production of different auto elements such as bumpers, grills, door panels, and control panel trim. The process gives an attire, regular outcome, enabling manufacturers to produce high-volume parts with great accuracy and marginal waste. The lightness of the extruded plastic components adds to the general reduction in automobile weight, improving gas effectiveness. In addition, the sturdiness and resistance of these components to heat, chilly, and influence boost the longevity of vehicles. Thus, plastic extrusion plays an essential function in vehicle manufacturing.
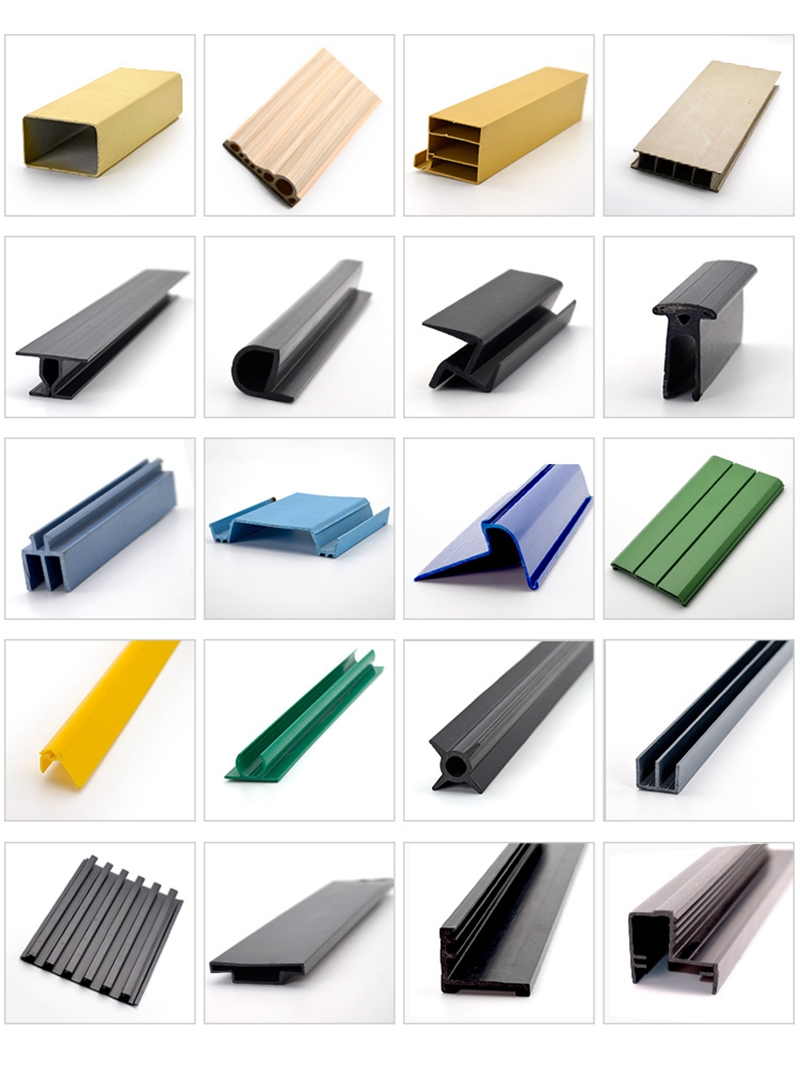
Applications of Plastic Extrusion in Customer Goods Production
Beyond its substantial influence on the vehicle industry, plastic extrusion confirms equally effective in the realm of durable goods manufacturing. This process is critical in producing a vast range of products, from food packaging to home devices, toys, and even clinical gadgets. The flexibility of plastic extrusion permits makers to design and create complex shapes and dimensions with high accuracy and effectiveness. In addition, due to the recyclability of numerous plastics, squeezed out components can be recycled, minimizing waste and cost. The flexibility, versatility, learn this here now and cost-effectiveness of plastic extrusion make it a preferred selection for several durable goods manufacturers, contributing substantially to the sector's growth and development. The environmental effects of this prevalent use require mindful factor to consider, visit homepage a topic to be gone over further in the succeeding section.
Environmental Influence and Sustainability in Plastic Extrusion
The prevalent use of plastic extrusion in manufacturing welcomes scrutiny of its eco-friendly ramifications. Effective equipment reduces power use, while waste monitoring systems reuse scrap plastic, decreasing raw product demands. Regardless of these enhancements, further development is required to reduce the environmental footprint of plastic extrusion.
Conclusion
To conclude, plastic extrusion plays a vital role in modern-day production, particularly in the automobile and durable goods fields. Its flexibility permits for the manufacturing of a variety of elements with high view it precision. Its possibility for recycling and advancement of biodegradable products uses an encouraging method towards lasting practices, therefore dealing with ecological problems. Comprehending the fundamentals of this process is essential to enhancing its applications and benefits.

The plastic extrusion procedure is extensively used in various sectors due to its cost-effectiveness, effectiveness, and flexibility.
Building upon the basic understanding of the plastic extrusion procedure, it is essential to explore the numerous methods involved in this production method. plastic extrusion. In comparison, sheet extrusion develops huge, flat sheets of plastic, which are usually additional refined right into items such as food packaging, shower curtains, and automobile components.An overwhelming bulk of parts in modern vehicles are products of the plastic extrusion procedure
Report this page